Discovering the Advantages of a Chemical Defoamer in Production and Production
The combination of chemical defoamers in manufacturing and production procedures provides a tactical advantage by dealing with one of the relentless obstacles in industrial operations: foam control. As suppliers make every effort to maximize processes and improve consumer fulfillment, the function of chemical defoamers comes to be increasingly crucial.
Value of Foam Control
While the presence of foam in producing procedures can occasionally seem safe, efficient foam control is essential for enhancing operational effectiveness and item quality. Foam can hinder different stages of manufacturing, bring about ineffectiveness that might boost expenses and prolong handling times. In markets such as food and drink, pharmaceuticals, and chemicals, unrestrained foam can obstruct equipment, interfere with automated systems, and eventually lead to item inconsistencies.
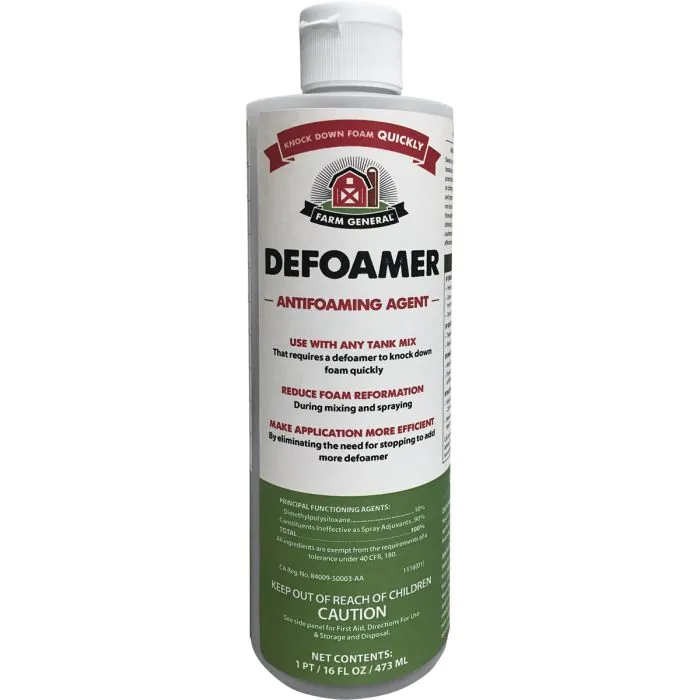
Implementing effective foam control techniques not only improves performance but additionally sustains regulative conformity in industries where foam can result in ecological issues. By utilizing chemical defoamers, manufacturers can mitigate these challenges, ensuring smoother procedures and higher-quality end products. Eventually, focusing on foam control is a vital aspect of production that can produce significant advantages in regards to effectiveness, safety and security, and item integrity.
Sorts Of Chemical Defoamers
What sorts of chemical defoamers are available for producing procedures, and exactly how do they vary in application? Chemical defoamers can be categorized right into three main types: silicone-based, organic, and inorganic defoamers. - Chemical Defoamer

Organic defoamers, usually stemmed from fatty acids or natural oils, work in a variety of applications, consisting of food and drink manufacturing. They are typically liked for their reduced poisoning and ecological impact, making certain compliance with sector policies.

Each kind of defoamer serves distinct purposes based on the chemical make-up and the particular requirements of the production process, permitting manufacturers to choose the most appropriate choice for their specific requirements.
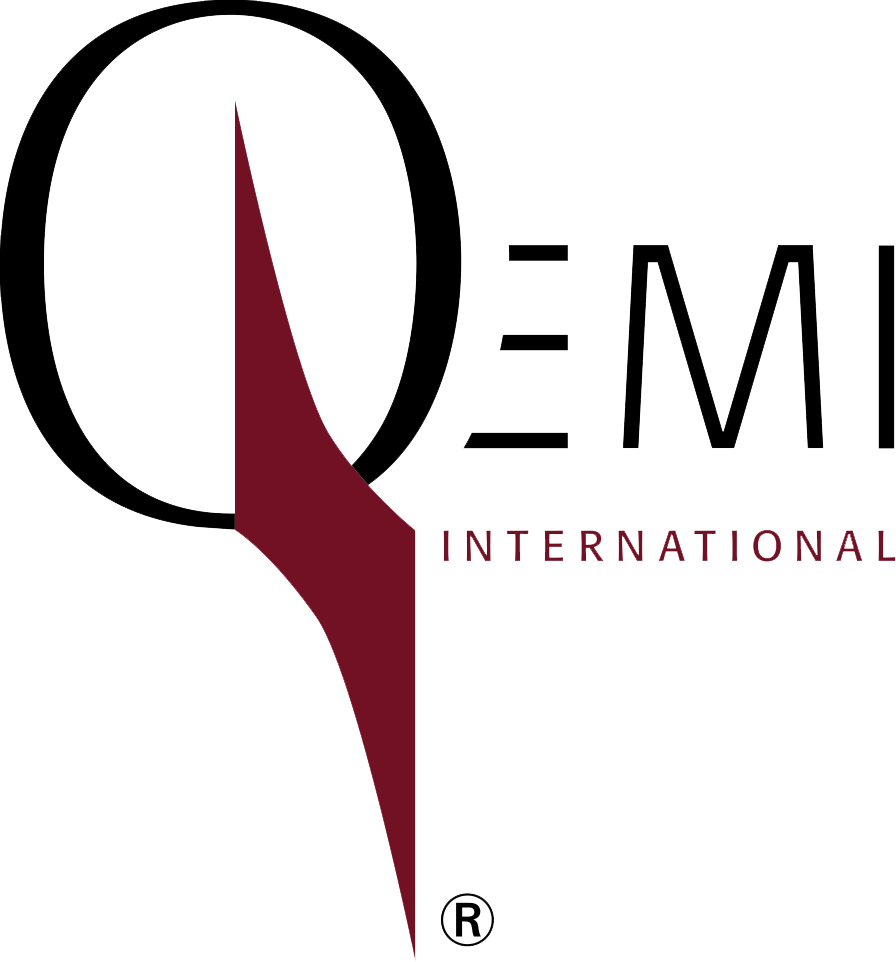
Advantages in Production Performance
Chemical defoamers play an important role in improving manufacturing performance by properly managing foam generation throughout numerous procedures. Foam can hinder manufacturing rates, interfere with devices procedure, and lead to costly downtime. By incorporating chemical defoamers, suppliers can reduce these concerns, making sure smoother workflow and boosted overall performance.
The use of chemical defoamers aids enhance the operational efficiency of tools such as reactors, mixers, and pumps. With minimized foam, these devices can operate at their intended capacity, minimizing the threat of overflow and allowing regular handling. This causes much better source usage and greater throughput.
Additionally, chemical defoamers help with faster processing times by lowering the time needed for foam elimination. This velocity can significantly influence manufacturing schedules, permitting makers to fulfill client demand click resources better. Additionally, making use of defoamers contributes to decrease energy intake, as equipment operates a lot more effectively with minimized foam interference.
Impact on Product High Quality
Foam control is not only essential for preserving performance in producing procedures but additionally plays site a considerable role in making certain item quality. Too much foam can present air into formulas, resulting in incongruities in the end product. This can manifest as issues such as gaps, unequal appearances, or below average surfaces, which threaten the intended top quality and performance of the item.
Furthermore, foam can prevent the homogeneity of combinations, resulting in uneven distribution of active components. In industries such as layers, cosmetics, and food manufacturing, this can result in variations in shade, taste, and overall effectiveness. By utilizing a chemical defoamer, makers can alleviate these risks, making certain that products satisfy strict high quality requirements.
Furthermore, controlling foam can boost the stability of suspensions and solutions, which is vital for making more sure shelf-life and consumer satisfaction. With improved product consistency and minimized flaws, suppliers can achieve higher requirements of quality assurance, eventually leading to increased client count on and brand name loyalty.
Cost-Effectiveness and ROI
Efficient foam control not just improves item quality but likewise adds dramatically to the general cost-effectiveness of producing processes. Making use of chemical defoamers minimizes foam-related issues, which can otherwise lead to production hold-ups, devices malfunctions, and enhanced energy intake. By decreasing foam, producers can enhance their procedures, bring about greater throughput and efficiency.
Purchasing chemical defoamers can yield a substantial return on financial investment (ROI) The initial costs connected with these additives are often countered by the savings recognized from reduced downtime and improved material yield. Boosted item top quality can lower waste and rework expenses, further reinforcing economic performance.
In addition, efficient foam control can bring about lowered water and energy usage, adding to reduced functional expenses. This is particularly essential in markets where resource effectiveness is paramount. By incorporating chemical defoamers right into their processes, suppliers can attain long-lasting financial savings while keeping competitive rates in the industry.
Final Thought
In conclusion, the assimilation of chemical defoamers in manufacturing and production procedures is important for maximizing functional efficiency and boosting product high quality. The advantages supplied by chemical defoamers not just support regulatory conformity but also offer an affordable side in the production landscape.
The integration of chemical defoamers in manufacturing and manufacturing processes provides a calculated advantage by attending to one of the persistent obstacles in industrial procedures: foam control.While the visibility of foam in producing processes can in some cases appear safe, effective foam control is critical for maximizing operational performance and item high quality.Chemical defoamers play a crucial role in enhancing making performance by efficiently regulating foam generation during various procedures.Moreover, chemical defoamers facilitate faster processing times by decreasing the time required for foam removal. Additionally, the usage of defoamers adds to reduce power consumption, as machinery runs extra successfully with minimized foam interference.